Pourquoi choisir l’Hydrodémolition ? Comparaison entre l’Hydrodémolition et les autres techniques de démolition de béton
Les avantages de l’Hydrodémolition sur la démolition classique par percussion (marteaux piqueurs hydraulique, pneumatique ou électrique) ou raboteurs sont les suivants :
- L’armature n’est pas détériorée. L’armature existante reste en place et n’est pas détériorée alors que le béton est détruit. Après l’Hydrodémolition robotisée, elle est parfaitement propre et prête à recevoir un nouveau béton.
- Pas de déplacement de l’armature. Dans la démolition par percussion, les vibrations peuvent déplacer les éléments de l’armature de façon sensible, ce qui entraîne une perte de résistance pour le béton restant.
- Le béton restant n’est pas détérioré. Le béton restant, lorsqu’il touche les zones détruites par des méthodes à percussion, est affecté de microfissures. Sa résistance en est réduite et, plus significatif, son adhérence au nouveau béton également.
- Adhérence améliorée. L’état des surfaces après Hydrodémolition est idéal pour l’adhérence du nouveau béton et l’adhérence est jusqu’à quatre fois supérieure à celle obtenue après destruction par percussion, grâce à l’utilisation de pressions ultra-hautes.
- Plus sûr pour les structures. Le jet d’eau découpe le béton par la pression de plusieurs bars qui agit comme un coin. À la différence des burins des démolisseurs, il n’endommagera pas d’éventuelles plaques de métal et ne produit pas de vibrations qui abîmeraient les structures rivetées. Sans poussière. L’Hydrodémolition élimine les poussières produites par la démolition classique, renforçant ainsi la sécurité sur le chantier.
Pas de nettoyage. Après l’Hydrodémolition, l’armature visible sera très propre. Il n’y a pas besoin de nettoyage final par grenaillage.
Considérations sur les équipements et la technique. L’Hydrodémolition repose sur l’emploi d’une pompe à pistons raccordée à une buse envoyant un jet d’eau à très haute ou ultra-haute pression. La capacité de démolition dépend des réglages de pression, du débit d’eau et de la résistance initiale du béton. L’option robotisée est idéale pour les gros volumes, tandis que la méthode manuelle à la lance offre une grande précision sur les chantiers exigus, garantissant l’excellence des travaux.
L’avantage le plus notable de l’Hydrodémolition sur la destruction par percussion réside dans sa capacité à enlever le béton sans causer de dommages à l’armature ni au béton voisin restant en place. Il en résulte que cette méthode est idéale, même pour des réparations partielles sur des ouvrages de bâtiment où il est nécessaire de faire une reprise sur l’armature existante.
Le jet d’eau se substitue de plus en plus au marteau-piqueur, source de nuisances (bruit, vibrations, poussières) facteur d’endommagement du ferraillage et générateur d’amorces de rupture, cause de propagation des fissures dans le béton, donc d’infiltration de l’eau avec risque de détérioration ultérieure par le gel. Dans certains pays l’usage du marteau-piqueur est déjà interdit sur les ponts et ouvrages d’art.
L’intérêt du jet hydrodynamique hydraulique est que la pression appliquée, mesurée en bars, étant supérieure aux contraintes de résistance du béton, un simple balayage manuel ou robotisé à la lance permet d’effectuer un véritable travail « de chirurgie » du béton tout en préservant les armatures et sans créer de vibrations dans les structures, garantissant la sécurité des supports.
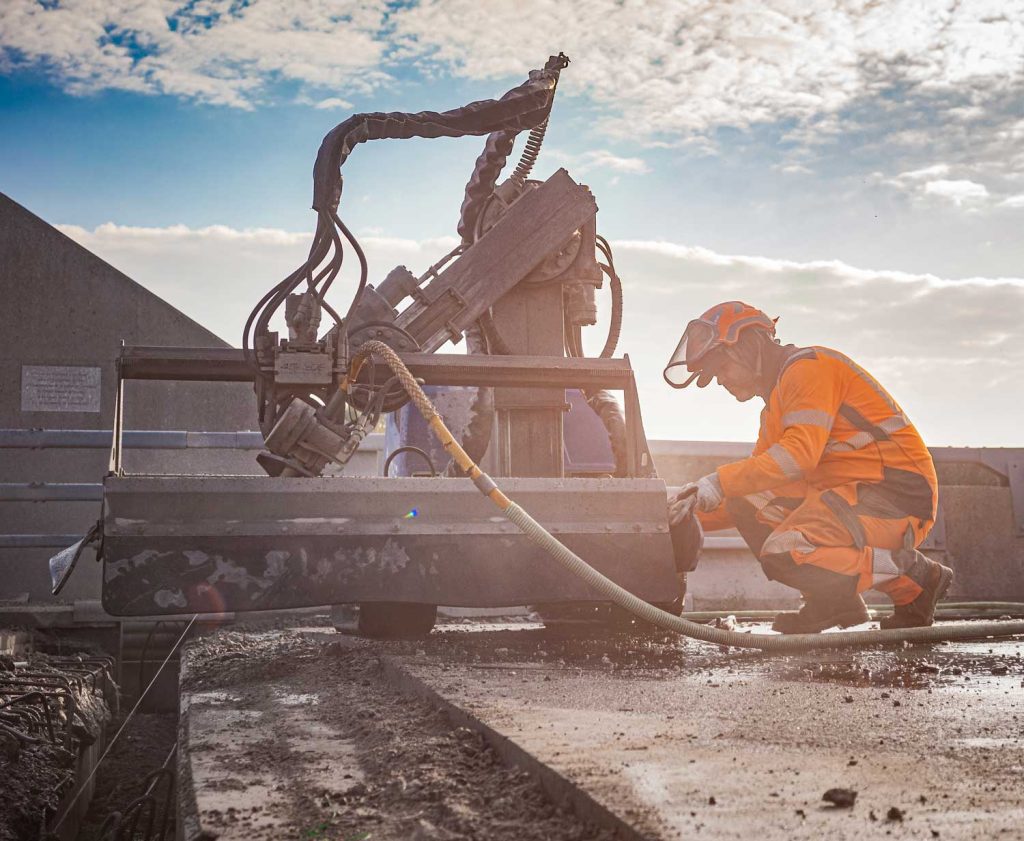
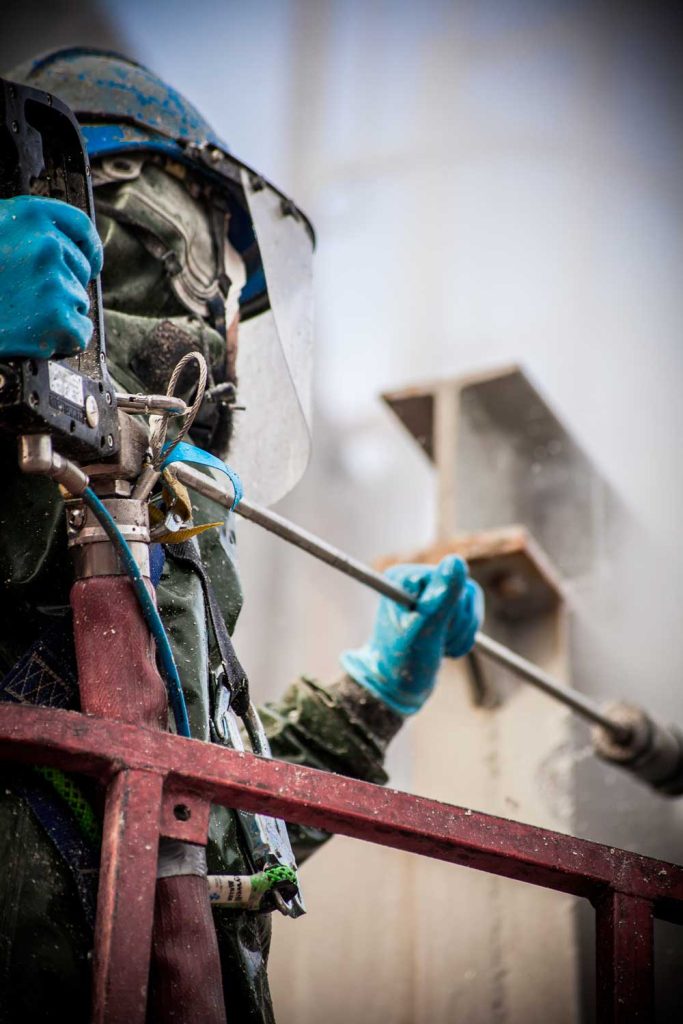