En quoi THP est-elle à la pointe des dernières technologies en matière d’hydrodémolition robotisée ?
THP s’est doté de l’Aquacutter 750V, qui bénéficie d’un nouveau système d’oscillation Infinity, breveté, et qui permet le déplacement de la lance du robot sous une pression ultra-élevée d’eau sur la forme géométrique de « l’infini ». Ces mouvements en « huit » permettent une plus grande efficacité de l’hydrodémolition en un seul passage en réduisant les zones d’ombres, également appelées zones résiduelles de béton sous les armatures métalliques. Mais ce n’est pas tout, l’hydrodémolition moderne chez THP offre également un avantage clé : l’absence de vibration lors de la destruction ciblée de surfaces de béton, un critère essentiel pour préserver les armatures métalliques et éviter les microfissures au sein du matériau.
Un nouveau niveau de performance grâce au système Evolution 3.0 et aux équipements d’hydrodémolition de THP
La dernière évolution du système de contrôle Evolution 3.0 constitue une nouvelle avancée en matière de gestion robotique informatisée pour les opérations d’hydrodémolition robotisée. L’interface du système de contrôle de l’Aquacutter 750V est interactive et montre sous forme de graphiques comment les paramètres tels que la pression de l’eau et les techniques d’hydrodémolition affecteront le fonctionnement du robot. Le réglage du système Infinity se calcule automatiquement grâce au système Evolution 3.0, via le pupitre de commande, optimisant ainsi les opérations sur chaque chantier.
En complément, il est important de souligner que l’intégration de tests de mise en pression systématique avant chaque démarrage de chantier garantit une mise en œuvre sécurisée. Cette étape comprend une vérification rigoureuse des équipements, des matériels de protection et des procédures pour prévenir tout incident. Cette démarche assure un résultat optimal tout en maintenant un niveau de sécurité et de protection supérieur, pour les équipes sur les chantiers et les infrastructures traitées.
L’oscillation Infinity – une productivité et une qualité de démolition accrues grâce aux techniques avancées de THP
En déplaçant la lance dans un double mouvement circulaire à Très Haute Pression (THP), au lieu d’un simple mouvement pendulaire pendant la phase d’oscillation, la forme du signe de « l’infini » apparaît… ou le chiffre « huit ». Ce mouvement de la lance rend la vitesse d’oscillation ultra-constante sur toute la surface tout au long du cycle de démolition.
Le calcul des vitesses de déplacements est un algorithme de plusieurs paramètres : la vitesse du chariot, la vitesse d’oscillation, la distance d’oscillation et de course de « l’infini ». Le nouveau système de contrôle du robot Evolution 3.0 se charge automatiquement de tous ces calculs et s’assure que la vitesse de surface est constante et linéaire pour un résultat inégalé.
De plus, grâce aux performances élevées des technologies d’hydrodémolition robotisée telles que l’oscillation Infinity, les surfaces préparées présentent une meilleure adhérence pour les traitements ou les réparations futures. Cette qualité accrue permet de prolonger la durabilité des infrastructures tout en augmentant la sécurité générale sur les chantiers.
L’oscillation Infinity permet d’avoir une surface beaucoup plus homogène grâce aux techniques d’hydrodémolition avancées par rapport à la lance oscillante standard. De plus, le rendement de démolition est plus élevé sur les sites industriels par rapport à la technologie précédente grâce à une vitesse de déplacement de la lance ultra-constante.
Un autre effet intéressant de l’oscillation Infinity est le bruit. Étant donné que le jet d’eau frappe continuellement le béton à la même vitesse, le bruit de pulsation est beaucoup moins important. Ce nouveau son est plus constant, moins alternatif, avec l’absence d’effet de crêtes.
Un signe de performance puisque le processus d’hydrodémolition se poursuit en permanence sans interruption. Une révolution !
Enfin, l’hydrodémolition permet de limiter les temps d’immobilisation des infrastructures sur les sites industriels.
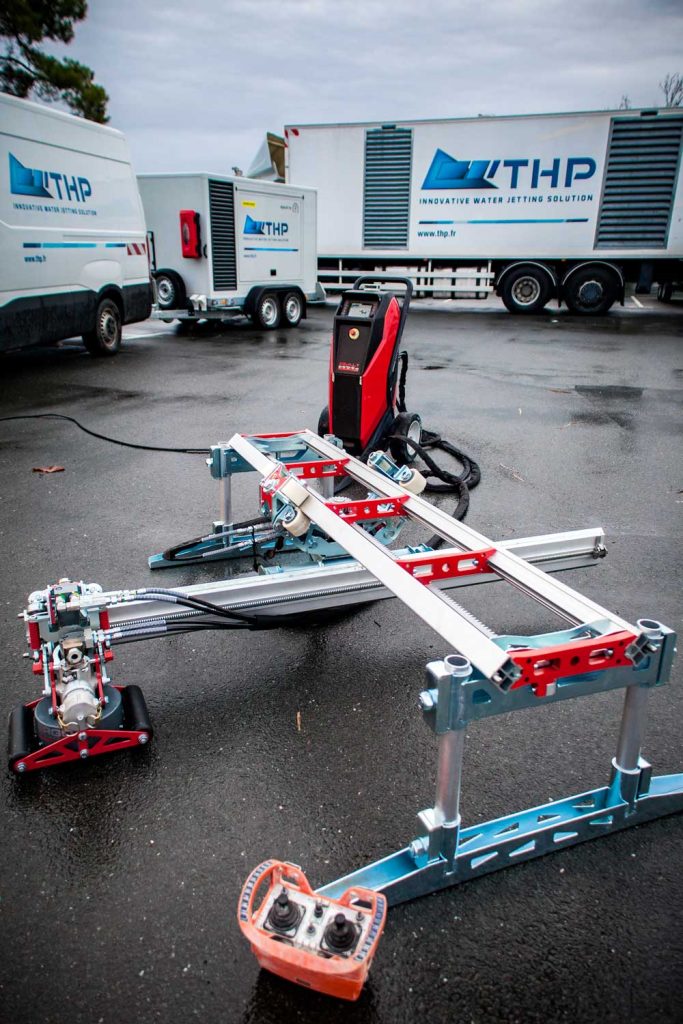
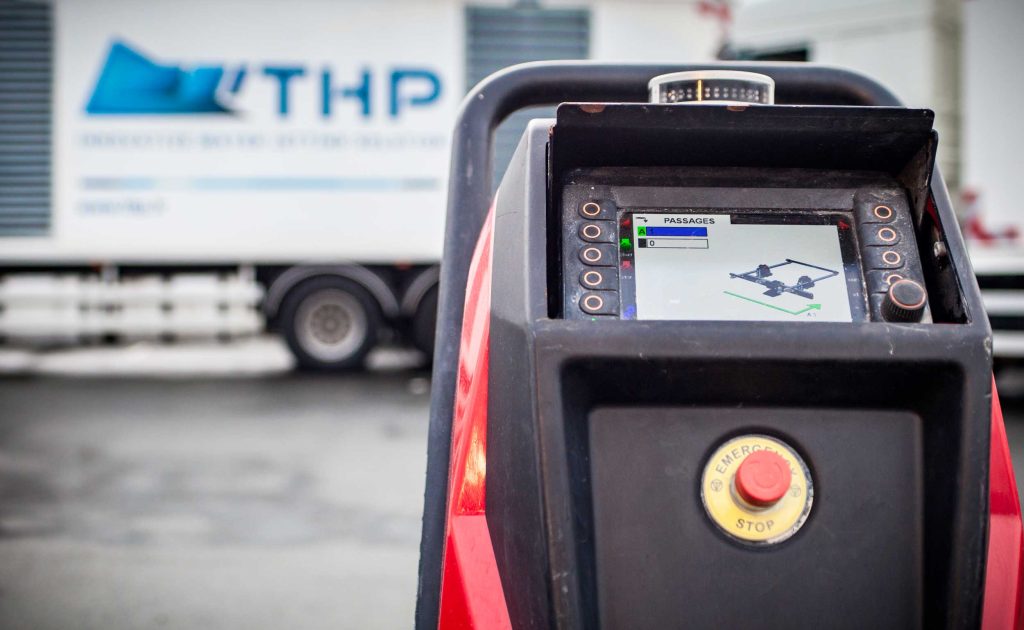